Kernkompetenz Leichtbau
Die Kernkompetenz Leichtbau zielt auf Nutzung von Kunststoffen in automobilen Bauteilen und Strukturen zur Reduzierung des Gewichts bei gleichzeitiger Verbesserung mechanischer und funktionaler Eigenschaften. Folgende Technologiefelder, die in zahlreichen Bereichen von Fahrzeugen zum Einsatz kommen, werden dabei verfolgt:
- Serienherstellungsverfahren für die Faserverbundtechnik
- Mehrkomponentenverfahrenstechnik
- Hybridbauteilherstellung, Verbindungstechnik, und Integrationstechniken für multifunktionale Baugruppen und
- Intelligente Kunststoffbauteile mit hoher Funktionsintegration
Arbeitsfelder
- Gewichtsreduzierende Struktur- und Antriebskomponenten
- Aufbau-, Füge- und Verbindungstechniken für Funktions- und Hochleistungs-Systeme
- Funktionalisierte Fahrzeugkomponenten, Werkstoffsysteme und Oberflächen
- Flexible, effizienzgesteigerte und serientaugliche Verarbeitungsprozessketten
- Umweltverträglichkeit und Verarbeitung nachwachsender Rohstoffe
- Material- und Prozesssimulationen zur Auslegung und Optimierung von Formteilen und Herstellungsverfahren
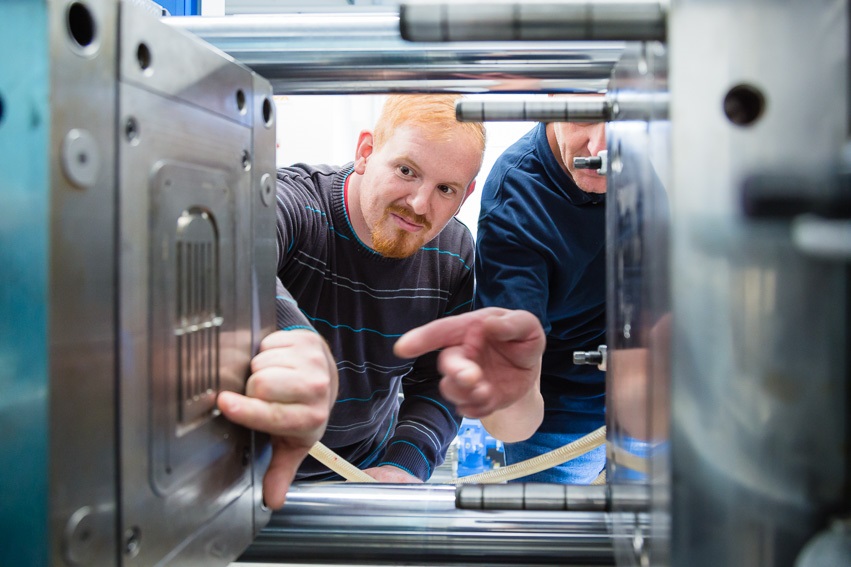
Referenzprojekt
VerDiOr – Entwicklung eines Verfahrens für die Herstellung direktextrudierter Organobleche mit Energieeinsparungsmöglichkeiten in einem vorindustriellen Umfeld
Projekt ansehenReferenzprojekt
Projektname
VerDiOr – Entwicklung eines Verfahrens für die Herstellung direktextrudierter Organobleche mit Energieeinsparungsmöglichkeiten in einem vorindustriellen Umfeld
Projektzeitraum:
1.01.2021 - 31.12.2022
Finanzierung:
Das Vorhaben wird im Rahmen des Programmes „Zentrales Innovationsprogramm Mittelstand“ (ZIM) unter dem Förderkennzeichen KK5007902EB0 vom Bundesministerium für Wirtschaft und Energie gefördert. Die Bewirtschaftung erfolgt durch das Thüringer Innovationszentrum Mobilität (ThIMo).
Projektkonsortium:
Folienwerk Wolfen GmbH, Bitterfeld-Wolfen; Technische Universität Ilmenau – Fachgebiet Kunststofftechnik
Kurzbeschreibung:
Endlosfaserverstärkte Thermoplaste, auch Organobleche genannt, vereinen die Vorteile der Umformbarkeit und der Rezyklierbarkeit thermoplastischer Kunststoffe mit den hervorragenden mechanischen Eigenschaften faserverstärkter Verbundwerkstoffe. Organobleche sind daher prädestiniert für die Substitution von Metallen und für die Fertigung funktionalisierter Bauteile im Spritzgießprozess.
Der konventionelle Herstellungsprozess von Organoblechen ist mit hohen Energiekosten verbunden, da aus dem Kunststoffgranulat zunächst Halbzeuge hergestellt werden. Ziel des Verbundprojektes „VerDiOr“ ist die Entwicklung eines energiesparenden Verfahrens zur Herstellung einlagiger Organobleche, bei dem der Kunststoff direkt in Granulatform verarbeitet werden kann. In Kooperation mit der Folienwerk Wolfen GmbH wird ein „Direktextrusionsverfahren“ weiterentwickelt und beim industriellen Projektpartner ein Prototyp im Produktionsmaßstab umgesetzt, der eine Herstellung von Organoblechen mit einer Breite von einem Meter unter seriennahen Bedingungen ermöglicht.
Vor der Realisierung des Prototyps werden an der Labormaschine des Fachgebiets Kunststofftechnik die zentralen Verarbeitungspunkte analysiert. Das Know-How beider Partner wird für die Entwicklung der Prototypenanlage kombiniert und die Erfahrungen und Simulationsergebnisse in ein Skalierungsmodell überführt. Ziel ist die Fertigung von Organoblechen mit maximalen Faservolumengehalt und hohen Durchsätzen im Produktionsmaßstab.
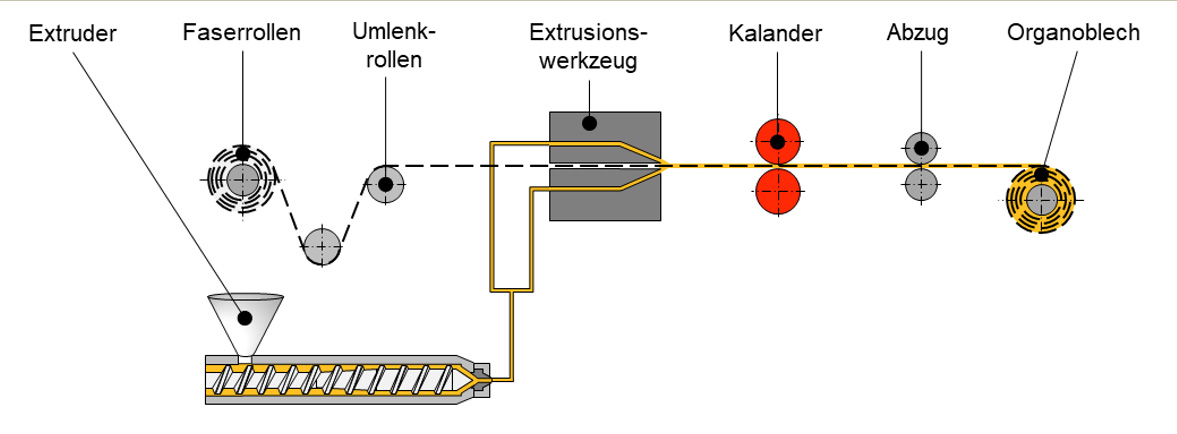
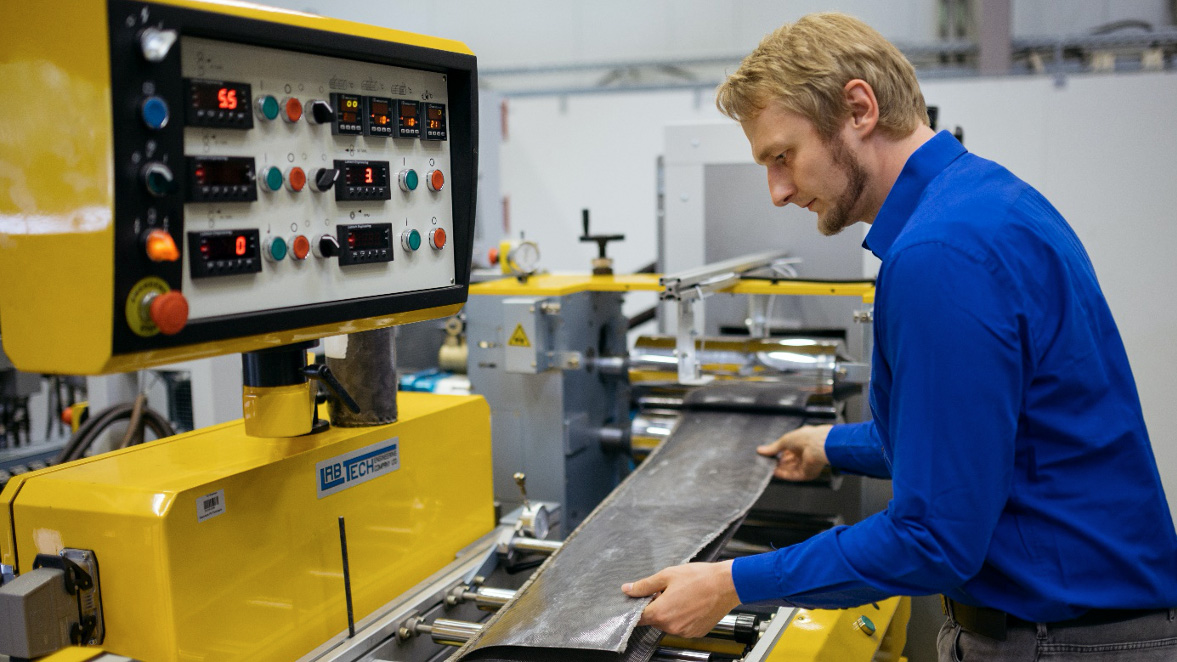
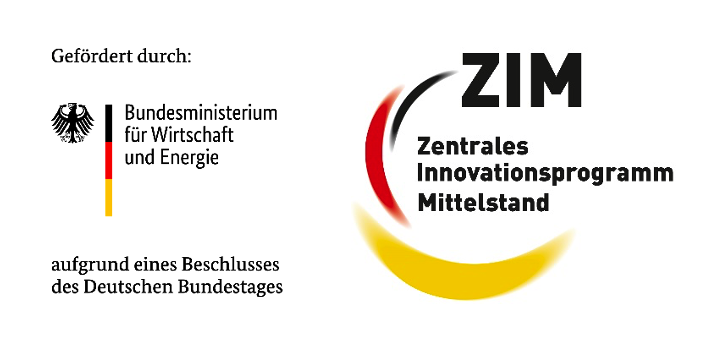